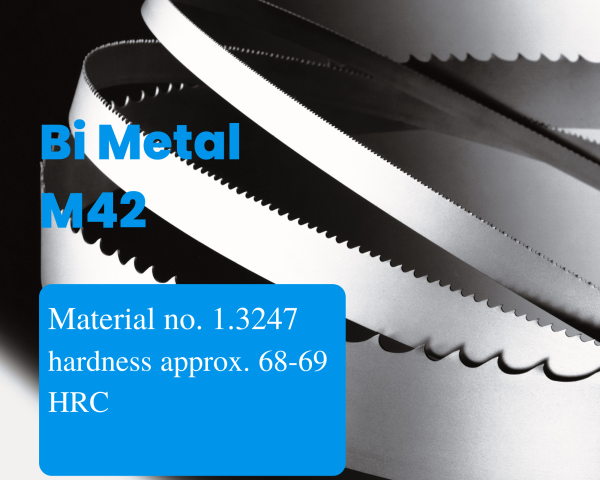
M42 Bi Metal Bandsaw Blades
Bi Metal bandsaw blade made of 4% high chrome alloyed backing material and a HSS cutting edge made of HSS M42 with s cobalt content of 8% each having teeth a hardness of 68-69 HRC combined with a tenacious backing material with high bending fatigue strength is ideal for cutting of all common steels grades up to a hardness of approx. 45 HRC in all diameters.
M42 BANDSAW BLADES DESCRIPTION
- High performance general purpose metal cutting blade.
- High Speed Steel cutting edge (8% cobalt and 10% molybdenum). Electron beam welded to a fatigue resistant tool steel backing.
- These features allow the blade to resist heat, shock and abrasion allowing faster cutting rates.
- These advantages result in more cost efficient cutting operations both for on-time applications and serial production.
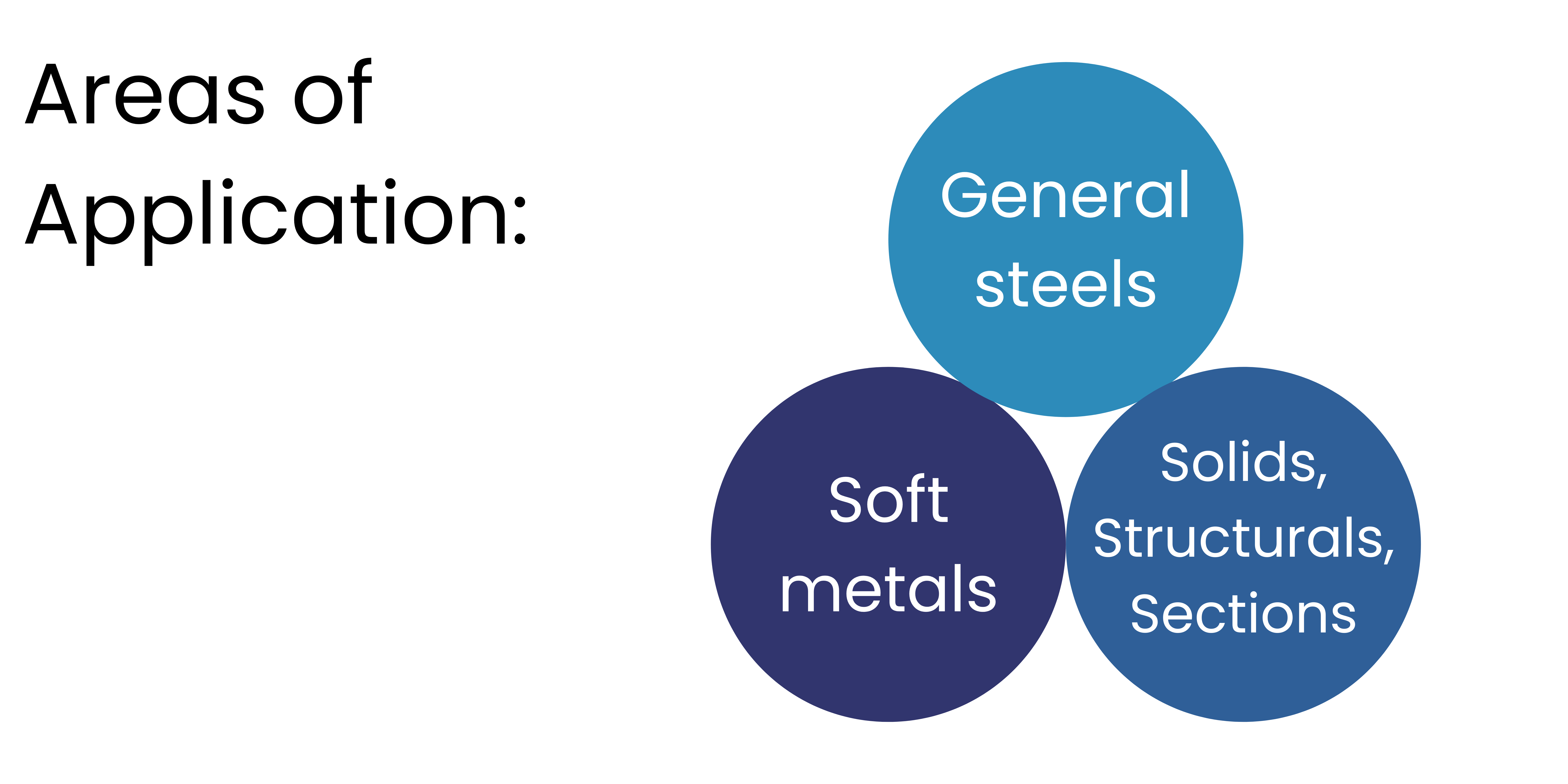
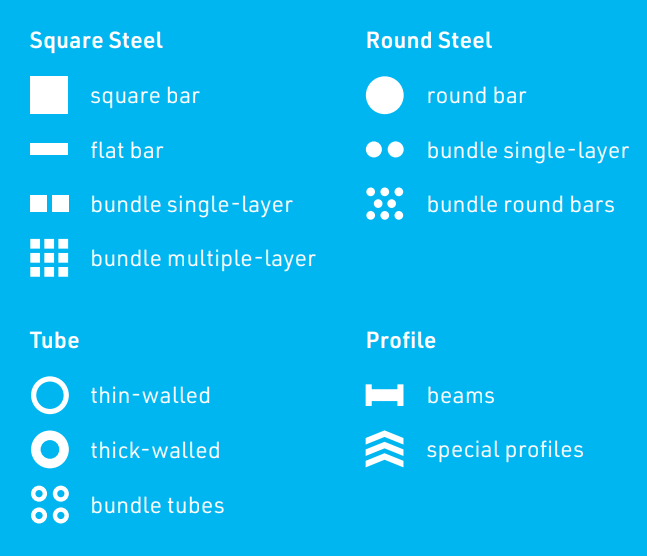
Features
1Flexibility
The blade backer of Bi Metal bandsaw blade consists of a special alloyed spring steel. highly flexible at a hardness of about 50 HRC.
2Hardness and wear resistance
Tooth tips made of hardened HSS steel quality obtained due to well-balanced hardening and fixed structure resulting in high wear resistance.
Band Saw Geometry:
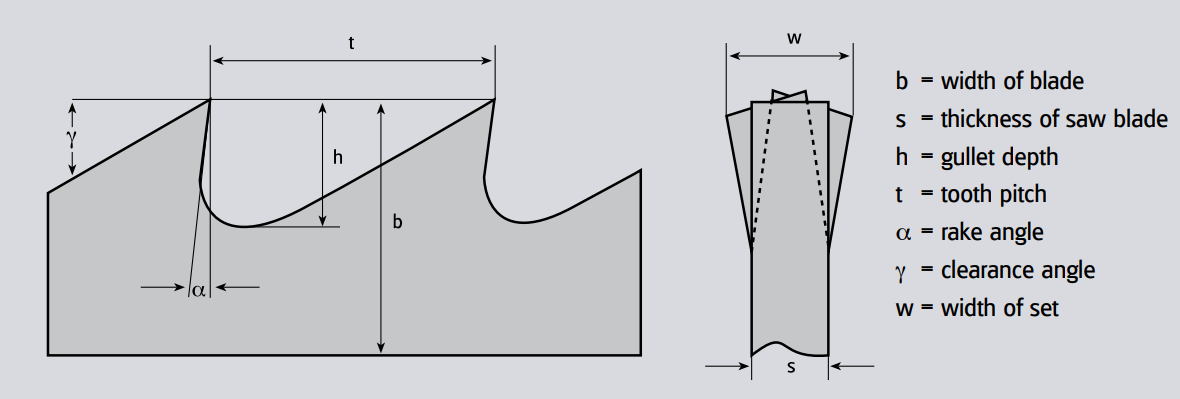
Tooth forms:
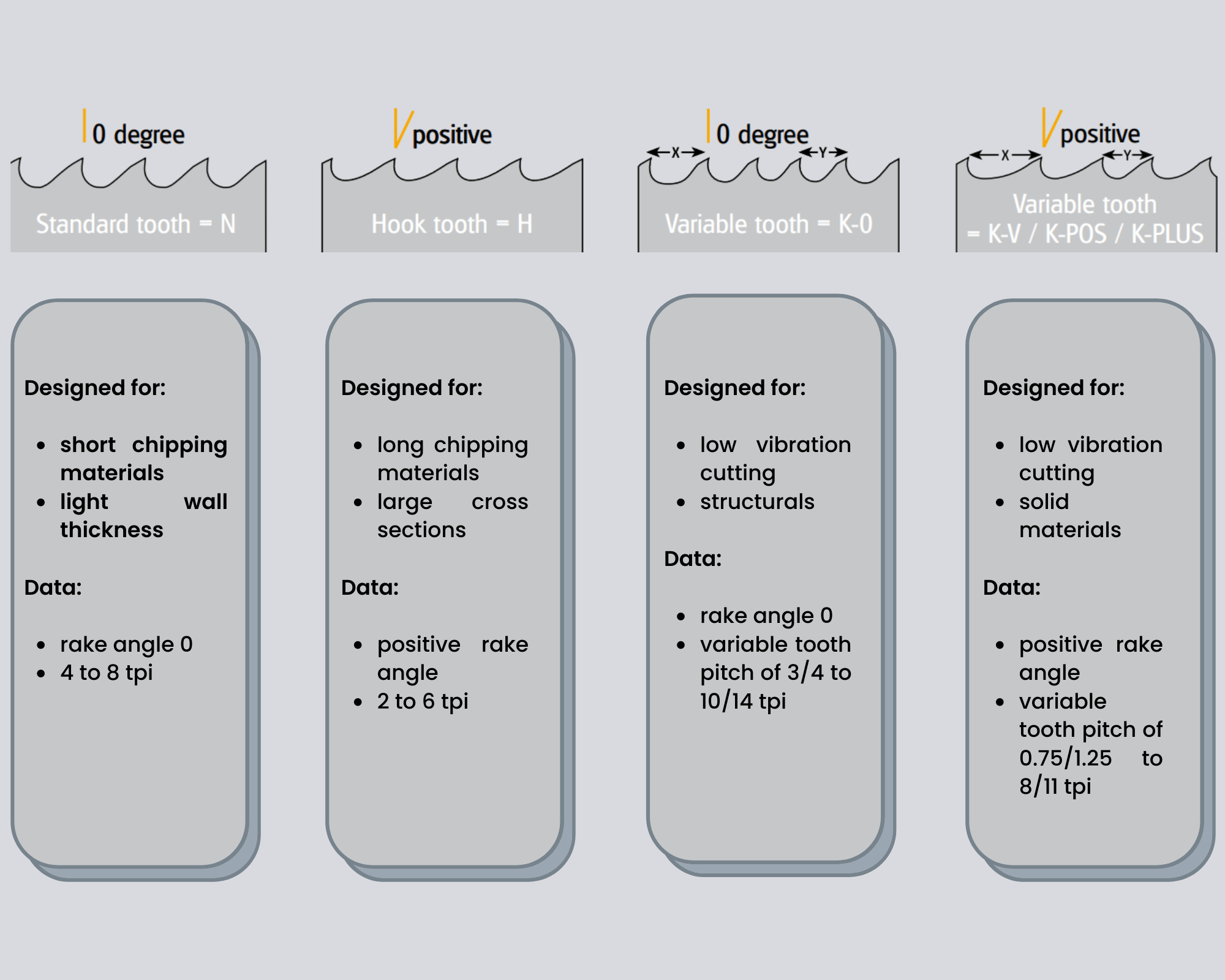
Tooth set
You must never ignore the importance of choosing the right tooth set, following section will help you gain information about about different types of sets on a band saw blade.
Recommendations For Tooth Selection
For Solide Material:
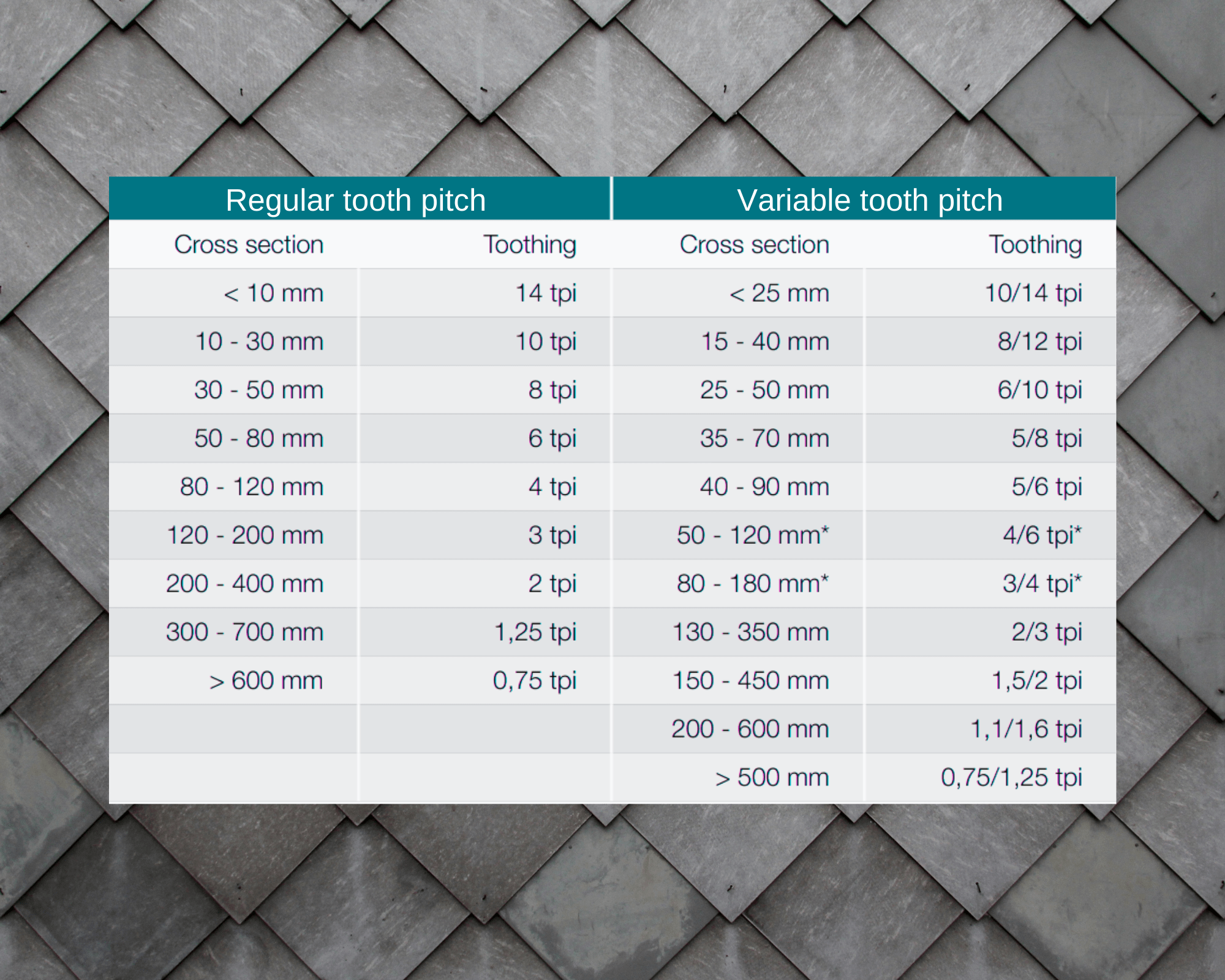
For Tubes:
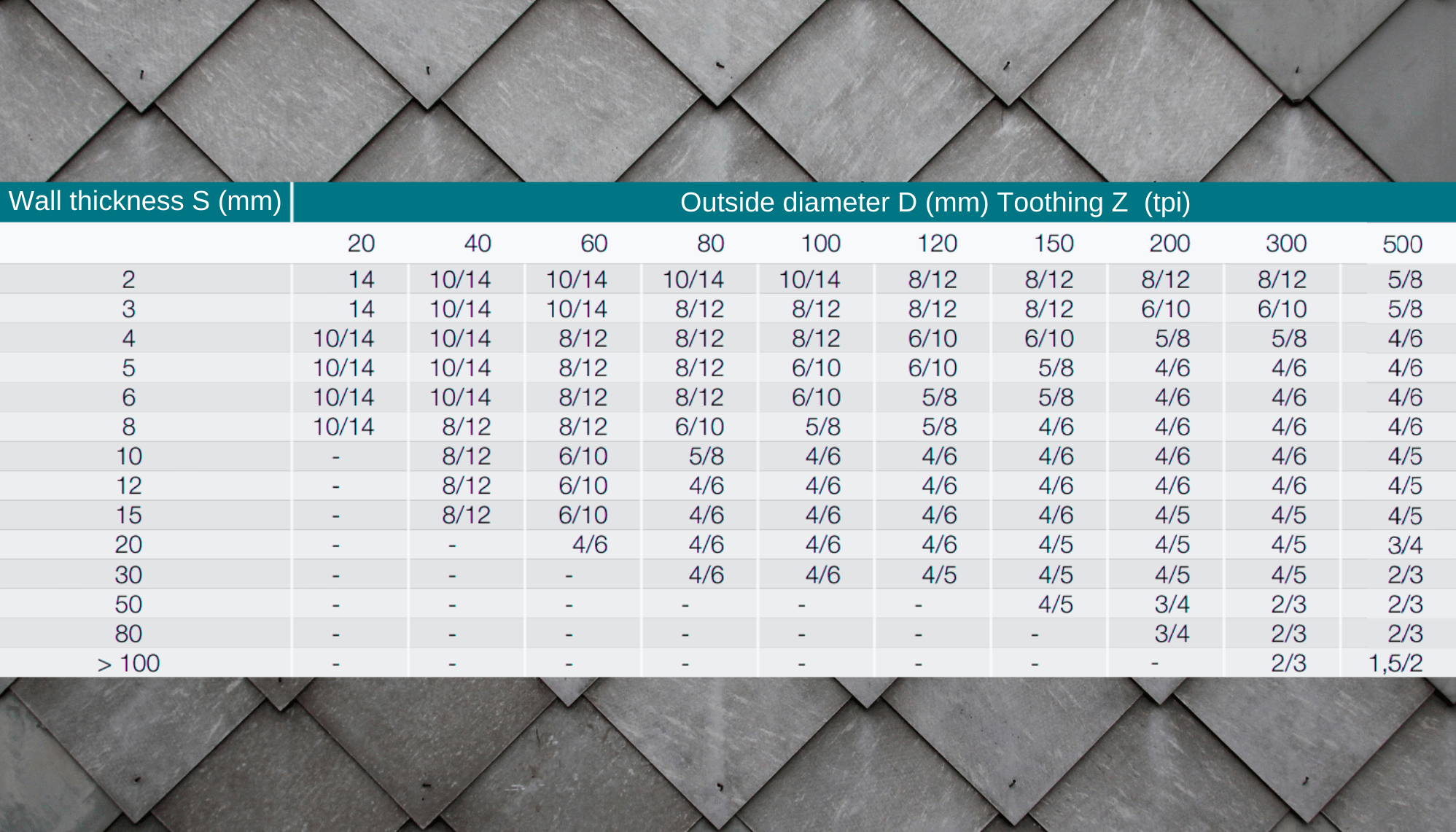
The choice of the right tooth has special influence on the cutting result on tubes and structurals. Variable tooth has provrn to be the most favorable tooth form. Tooth pitches selection depend on wall thickness and outer dimensions of tubes or structurals. The recommendations shown here refer to single cuts. If two or more tubes or square pipes are cut at a time, double wall thickness to select tooth pitch.
Different Sizes of Bandsaw Blades Production
To obtain optimum cutting rates, tooth pitch and tooth design are of great importance. we offer various tooth pitches to solve your cutting problems.
mm | 3 | 4 | 6 | 8 | 10 | 14 | 0.75/1,25 | 1,4/2 | 2/3 | 3/4 | 4/6 | 5/8 | 6/10 | 8/12 | 10/14 |
---|---|---|---|---|---|---|---|---|---|---|---|---|---|---|---|
6 * 0.90 | |||||||||||||||
10 * 0.90 | |||||||||||||||
13 * 0.65 | |||||||||||||||
13 * 0.90 | |||||||||||||||
20 * 0.90 | |||||||||||||||
27 * 0.90 | |||||||||||||||
34 * 1.10 | |||||||||||||||
41 * 1.30 | |||||||||||||||
54 * 1.30 | |||||||||||||||
54 * 1.60 | |||||||||||||||
67 * 1.60 | |||||||||||||||
80 * 1.60 |
: 0 rake angle tooth type is particularly suited for cutting short chipping, low alloyed materials, solids in small and medium cross sections as well as tubes and profiles.
: Positive rake angle of 10 or 16, the hook tooth has a large, long-drawn-out chip space. Therefore, it is mostly used for cutting non-ferrous metals, steels with a low content of carbon, Cr-Ni alloys, and primarily bigger cross sections.
: Both 0 and positive rake angles possible